New Arburg IMM to help scale EcoCore packaging moulds for world-leading brands and converters
- News editor
- Apr 17
- 2 min read
Updated: 2 days ago
The new larger injection moulding machine (IMM) will be used with multi-cavity high-capacity packaging moulds due for delivery this year. The continued support from ARBURG for Bockatech and EcoCore® comes as the innovative foamtech is increasingly recognised as improving sustainability and enhancing performance without sacrificing profitability.

Describing the importance of the new ARBURG machine, Henri Gaskjenn, CEO at Bockatech, says: “EcoCore is a proven technology and our focus now is producing more mouldings at a greater scale.
"We are very grateful to ARBURG. Our clients are world-leading brands as well as converters, and the new IMM will allow them to see their new EcoCore high-capacity multi-cavity moulds running at full speed before delivery.
"The IMM will also be used for new single-use food and non-food packaging applications for some major brands, as pressure grows for them to meet internal ESG objectives and new packaging legislation."
The new ARBURG ALLROUNDER 820H Packaging IMM will be used by the Bockatech R&D team based in the UK
Talking about ARBURG's support for Bockatech, Markus Haas, Packaging Sales Manager at ARBURG, comments: "Moulding solutions that improve sustainability are a key commitment for ARBURG. We're delighted to continue supporting EcoCore as its sustainability benefits and ability to manufacture are proven and it's used for higher-capacity moulds.
"The new ALLROUNDER 820H P is larger and complements the smaller ALLROUNDER 520A that Bockatech already uses for product development.
"With the same rich feature set as the 520A, essential for the EcoCore process, the 820H P offers fast opening times and precision control. Its seamless integration with chemical and physical gas sources, along with robotics for labelling and take off, makes it an ideal choice.”
The machine will be part of a complete manufacturing cell needed to make EcoCore mouldings with physical gas as well as foaming agent. The cell will also feature robotics for part takeoff, stacking and in mould labelling (IML) eventually.
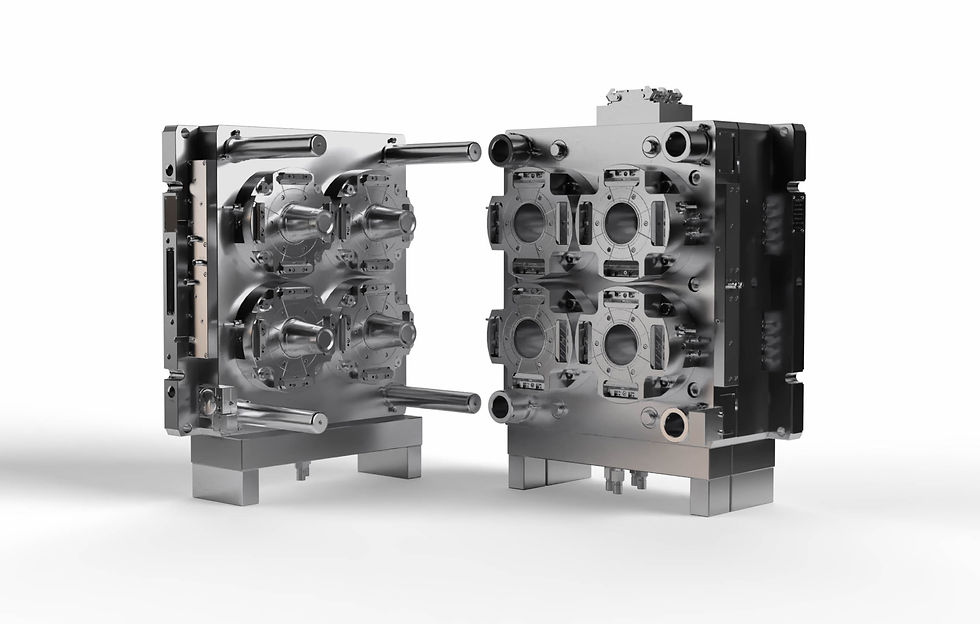
“The new IMM and cell also provide a blueprint for a proven manufacturing setup that brands and converters can quickly and easily use in their production facilities,” concludes Haas.
Comments